Steel remains one of the most versatile materials in construction and manufacturing, thanks to its unmatched strength and durability. The melting point of steel is a critical factor that significantly influences its performance in extreme conditions. In this article, we delve into the science behind steel's melting point, explore its variations, and examine how it shapes various industries.
Steel's melting point is a defining characteristic that determines its usability in high-temperature environments. Engineers and architects depend on this information to ensure safety and efficiency in countless projects. A thorough understanding of this property is essential for professionals working with steel, as well as students studying material science.
This article aims to provide a comprehensive exploration of steel's melting point, its importance, and related factors. Backed by reliable data and expert insights, it serves as a valuable resource for readers seeking a deeper understanding of this critical material property.
Read also:Naughty America The Ultimate Guide To The Worlds Largest Adult Entertainment Empire
Table of Contents
- Understanding Steel's Melting Point
- The Role of Composition in Determining Steel's Melting Point
- Variations in Melting Points Across Steel Types
- Applications of Steel Based on Melting Point
- The Science Behind Steel's Melting Point
- Methods for Testing Steel's Melting Point
- Comparing Steel's Melting Point with Other Metals
- Steel's Role in Key Industries
- Safety Considerations in High-Temperature Applications
- Future Innovations in Steel Technology
Understanding Steel's Melting Point
The melting point of steel refers to the temperature at which it transitions from a solid to a liquid state. This property is crucial in determining steel's suitability for specific applications, particularly in environments where high temperatures are a concern. Steel's melting point typically ranges between 1370°C and 1510°C (2500°F to 2750°F), depending on its composition. Engineers and manufacturers rely on this information to design products and structures that can withstand extreme conditions.
Why is the Melting Point of Steel Significant?
The melting point of steel plays a pivotal role in its performance under high-temperature scenarios. For instance, in construction, understanding steel's melting point ensures the structural integrity of buildings during emergencies such as fires. Similarly, in the automotive and aerospace industries, it guarantees the reliability of components exposed to intense heat. This knowledge empowers engineers to make informed decisions, enhancing both safety and efficiency.
The Role of Composition in Determining Steel's Melting Point
Steel is an alloy primarily composed of iron and carbon, with varying amounts of other elements like chromium, nickel, and manganese. These additional elements significantly influence the melting point of steel, allowing it to be tailored for diverse applications.
Key Elements and Their Impact on Melting Point
- Carbon: While carbon increases the hardness of steel, it also lowers its melting point. This trade-off allows manufacturers to balance strength and heat resistance.
- Chromium: Chromium enhances corrosion resistance and slightly raises the melting point, making it ideal for applications requiring both durability and heat tolerance.
- Nickel: Nickel improves toughness but may slightly decrease the melting point. Its inclusion is often balanced with other elements to achieve optimal performance.
By carefully adjusting the composition, manufacturers can produce steel grades that meet specific needs, ensuring a harmonious balance of properties such as strength, ductility, and heat resistance.
Variations in Melting Points Across Steel Types
Steel comes in many forms, each with distinct properties and melting points. Below are some common types:
Carbon Steel
Carbon steel, which contains up to 2.1% carbon, has a melting point ranging from 1425°C to 1540°C (2597°F to 2804°F). Its simplicity and affordability make it a popular choice in construction and manufacturing, where cost-effectiveness is a priority.
Read also:Ana Kasparian A Rising Star In Sports Journalism And Beyond
Stainless Steel
Stainless steel, renowned for its corrosion resistance, melts between 1400°C and 1450°C (2552°F to 2642°F). The addition of chromium and nickel not only enhances its resistance to oxidation but also increases its ability to withstand high temperatures.
Tool Steel
Tool steel, designed for high-strength applications, typically melts at temperatures above 1400°C (2552°F). Its unique alloying elements ensure exceptional durability and heat resistance, making it ideal for demanding environments.
Applications of Steel Based on Melting Point
The melting point of steel dictates its suitability for various applications. Below are some examples:
Construction Industry
In the construction sector, steel's melting point ensures the stability of structures during emergencies such as fires. Engineers design buildings with steel components capable of withstanding temperatures close to their melting point, providing critical time for evacuation and minimizing structural damage.
Automotive Industry
Automobile manufacturers utilize steel with appropriate melting points to produce engine parts and structural components. These parts must endure high temperatures without compromising performance or safety, ensuring the longevity and reliability of vehicles.
The Science Behind Steel's Melting Point
The melting point of steel is determined by the bonds between its atoms. In steel, the iron atoms form a crystalline structure, and the presence of alloying elements modifies these bonds, influencing the melting point.
Factors Affecting Steel's Melting Point
- Atomic Structure: The arrangement of atoms in steel plays a significant role in determining its melting point. Variations in atomic structure can lead to differences in thermal stability.
- Thermal Conductivity: Steel's ability to conduct heat affects how quickly it reaches its melting point. Materials with higher thermal conductivity tend to melt more rapidly.
- Impurities: Even small amounts of impurities can lower the melting point of steel, necessitating precise control during manufacturing processes.
Understanding these factors enables scientists and engineers to develop advanced steel grades with optimized melting points, tailored to meet the demands of specific applications.
Methods for Testing Steel's Melting Point
Several techniques are employed to determine the melting point of steel:
Thermocouple Measurement
Thermocouples are widely used to measure the temperature of steel during the melting process. This method provides accurate readings and is commonly utilized in industrial settings to ensure precise data collection.
Differential Scanning Calorimetry (DSC)
DSC involves heating a sample of steel and monitoring the energy changes during the melting process. This technique is particularly effective for analyzing small samples and obtaining highly precise data, making it invaluable in research and development.
Comparing Steel's Melting Point with Other Metals
Steel's melting point surpasses that of many other metals, making it an ideal choice for high-temperature applications. Below is a comparison:
Melting Points of Common Metals
- Iron: 1538°C (2800°F)
- Aluminum: 660°C (1220°F)
- Copper: 1085°C (1985°F)
Steel's higher melting point offers a distinct advantage in industries where materials must withstand extreme heat, ensuring superior performance and reliability.
Steel's Role in Key Industries
Steel's melting point plays a critical role in numerous industries:
Aerospace Industry
In aerospace, steel components must endure high temperatures during flight. Engineers carefully select steel grades with appropriate melting points to ensure the reliability and safety of aircraft, even under the most demanding conditions.
Energy Sector
Steel is extensively used in power plants and oil refineries, where high temperatures are commonplace. Its melting point ensures the longevity and efficiency of equipment, contributing to the overall success of these industries.
Safety Considerations in High-Temperature Applications
When utilizing steel in high-temperature applications, safety is paramount. Proper design and material selection are essential to prevent failures that could result in catastrophic consequences.
Preventive Measures
- Regular Inspections: Steel components should be inspected regularly for signs of wear or damage, ensuring timely maintenance and minimizing risks.
- Temperature Monitoring: Implementing systems to continuously monitor temperatures and alert operators of potential issues is crucial for maintaining safety and efficiency.
By prioritizing safety, industries can maximize the benefits of steel while minimizing risks, ensuring long-term success and reliability.
Future Innovations in Steel Technology
Advancements in steel technology continue to enhance its properties, including its melting point. Researchers are exploring new alloy compositions and manufacturing techniques to create steel grades with improved heat resistance.
Emerging Trends in Steel Development
- Nanosteel: Incorporating nanotechnology into steel production offers the potential to improve its strength and melting point, opening new possibilities for advanced applications.
- Advanced Alloying: Developing innovative combinations of elements allows engineers to achieve desired properties, further expanding the capabilities of steel in various fields.
These innovations promise to revolutionize the applications of steel, solidifying its importance in modern industries and paving the way for future advancements.
Conclusion
In conclusion, the melting point of steel is a critical property that profoundly influences its performance and applications. By understanding the factors affecting its melting point and the underlying science, we can effectively harness steel's potential while ensuring safety and efficiency. Whether in construction, automotive, aerospace, or energy sectors, steel's melting point remains a cornerstone of reliability and innovation.
We encourage you to share your thoughts and experiences with steel in the comments below. Additionally, explore our other articles for more insights into materials science and engineering. Together, let's continue advancing our knowledge and application of steel in various fields, driving progress and innovation forward.
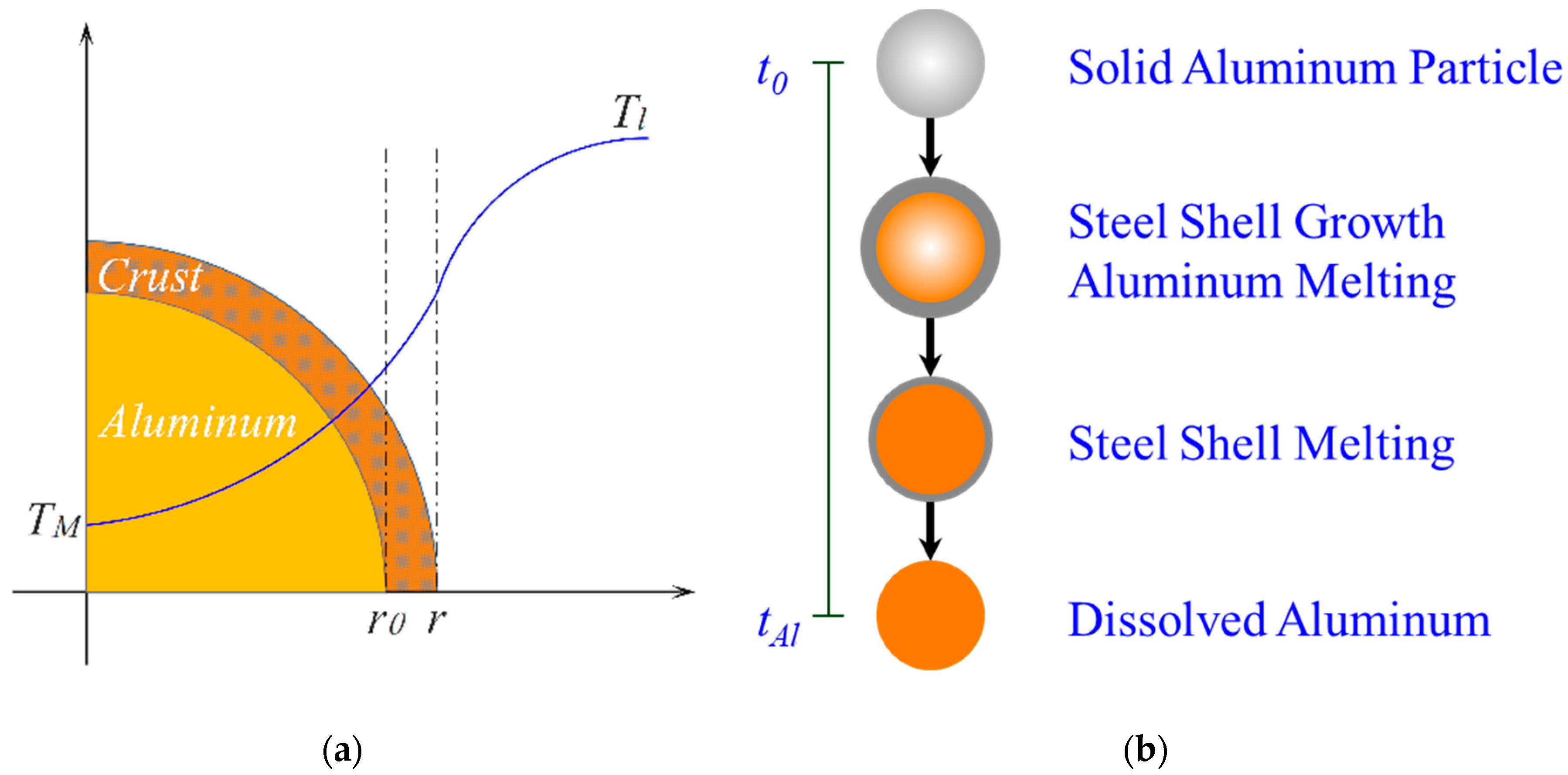
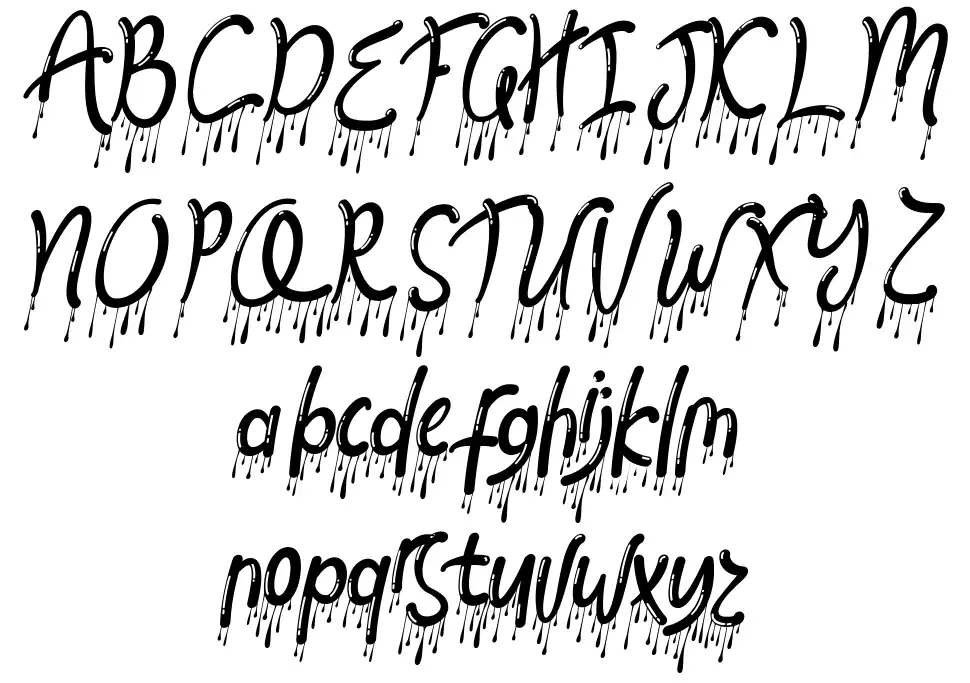
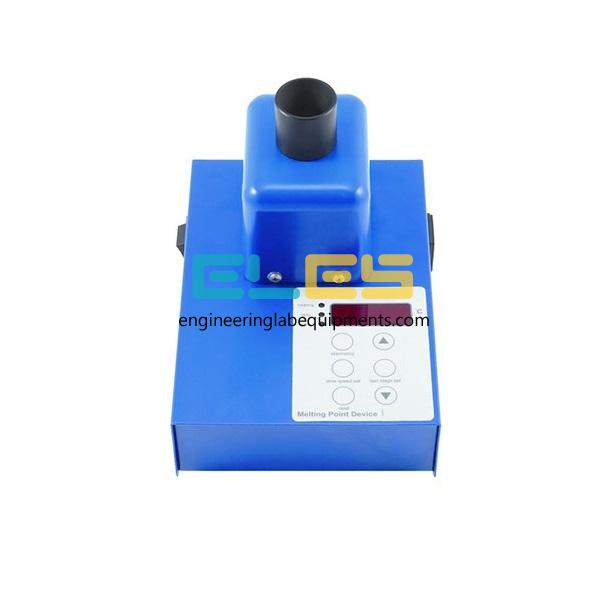